Filetti, scanalature e fori: ecco come si lavorano i metalli
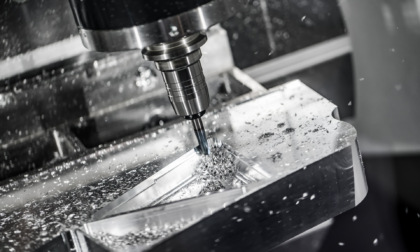
Di fronte al forte sviluppo di tecnologia ed informatica degli ultimi anni, i macchinari meccanici ricoprono ancora un importante ruolo nella realizzazione di particolari meccanici di precisione. Tanto che i processi automatizzati hanno portato tecnologia e meccanica a fondersi: due facce della stessa medaglia che non possono sopravvivere una senza l’altra.
Il risultato è la produzione di particolari meccanici, che sono il frutto dell’ingegno dell’uomo: elementi costruiti e realizzati che necessitano di una serie di componenti da montare assieme. Ogni progetto è a sé: si parte sempre da zero quando si costruiscono macchinari per i settori più disparati, da quello alimentare a quello delle macchine da cucire, dagli strumenti per la lavorazione del marmo fino alla strumentazione nautica o per l’astronomia.
Nell’ambito della meccanica di precisione si inseriscono diverse tipologie di lavorazioni che richiedono competenza, professionalità e precisione, in quanto anche il più piccolo dei componenti meccanici può incidere negativamente, se non ben realizzato, sul funzionamento finale dei macchinari nei quali verranno impiegati. Queste lavorazioni possono variare a seconda della tipologia di componente da realizzare, delle caratteristiche geometriche e dimensionali e del materiale scelto. Tra le principali troviamo la fresatura e la tornitura.
In cosa consiste la tornitura?
Anche gli apparecchi più grandi sono realizzati assemblando pezzi più piccoli – a volte anche piccolissimi – tenuti insieme da viti, cilindri, bulloni. Si tratta di elementi di componentistica, che non sempre sono standard ma richiedono una personalizzazione in base alla macchina che si sta realizzando. E’ soprattutto in questi casi che le officine meccaniche di precisione ricorrono alle lavorazioni di tornitura dei metalli, ovvero l’atto con cui si lavora il materiale limandolo e asportandone il truciolo fino ad avere la sagoma che si desidera. E’ questo il metodo utilizzato per creare anche fori e scanalature, atte ad ospitare viti o altri elementi di congiuntura, oppure in grado di permettere l’incastro fra due o più parti di metallo.
Lo strumento utilizzato per ottenere questa tipologia di lavorazione è ovviamente il tornio, uno dei più antichi ideati dall’essere umano, oggi ovviamente meccanizzato.
La tornitura prevede una lavorazione di questo tipo: si passa da una prima fase di lavorazione grossolana, attraverso la quale viene eliminata la maggior parte del materiale che non serve, fino alla rifinitura, quando si riesce a creare fori o scala nature di misure precise nell’ordine dei millimetri.
I materiali più utilizzati in tornitura
La tornitura viene solitamente effettuata su quei materiali che non è possibile lavorare a mani nude, come appunto i metalli: acciaio inox e acciai austenici, per esempio, ma anche alluminio, bronzo e ottone, fino ad arrivare alle plastica. Anche la plastica non è un materiale facile da tagliare, forare e ridimensionare; servono strumenti in grado di modellarne la superficie senza però riportare danni che rischiano di rendere il materiale inutilizzabile.
La fresatura: il completamento del lavoro
In molti casi, le officine meccaniche possono impiegare insieme fresatura e tornitura per produrre specifici particolari finiti. Infatti, pur essendo lavorazioni diverse, la fresatura presenta alcuni aspetti simili e complementari alla tornitura. L’impiego simultaneo della fresa e del tornio è stato possibile soprattutto grazie all’evoluzione tecnologica che ha dato vita ai cosiddetti centri di lavoro multitasking.
Durante il processo di fresatura, infatti, la fresa ruota ad alta velocità e viene spinta contro il materiale di lavoro, creando tagli o scanalature sulla superficie. Grazie alla sua capacità di rimuovere materiale con precisione e accuratezza, questa tipologia di lavorazione consente la produzione di componenti con tolleranze molto strette e finiture superficiali di alta qualità.
E’ considerata la fase finale per la rifinitura più precisa, ma con il tempo però sono stati creati macchinari sempre più sofisticati in grado di affrontare entrambe le operazioni permettendo di ridurre i tempi di lavorazione e, di conseguenza, anche i costi, sia di personale sia in termini di investimento di strumenti.